Electrify: Accelerating Electric Vehicle Production with Digital Twin Technology
The automotive industry is undergoing a seismic shift towards electric vehicles (EVs). This transition presents both exciting opportunities and significant challenges for manufacturers. Electrify, a fictional car manufacturer, faced the daunting task of scaling EV production while maintaining quality and navigating a complex supply chain. To overcome these hurdles, Electrify embraced digital twin technology, transforming […]
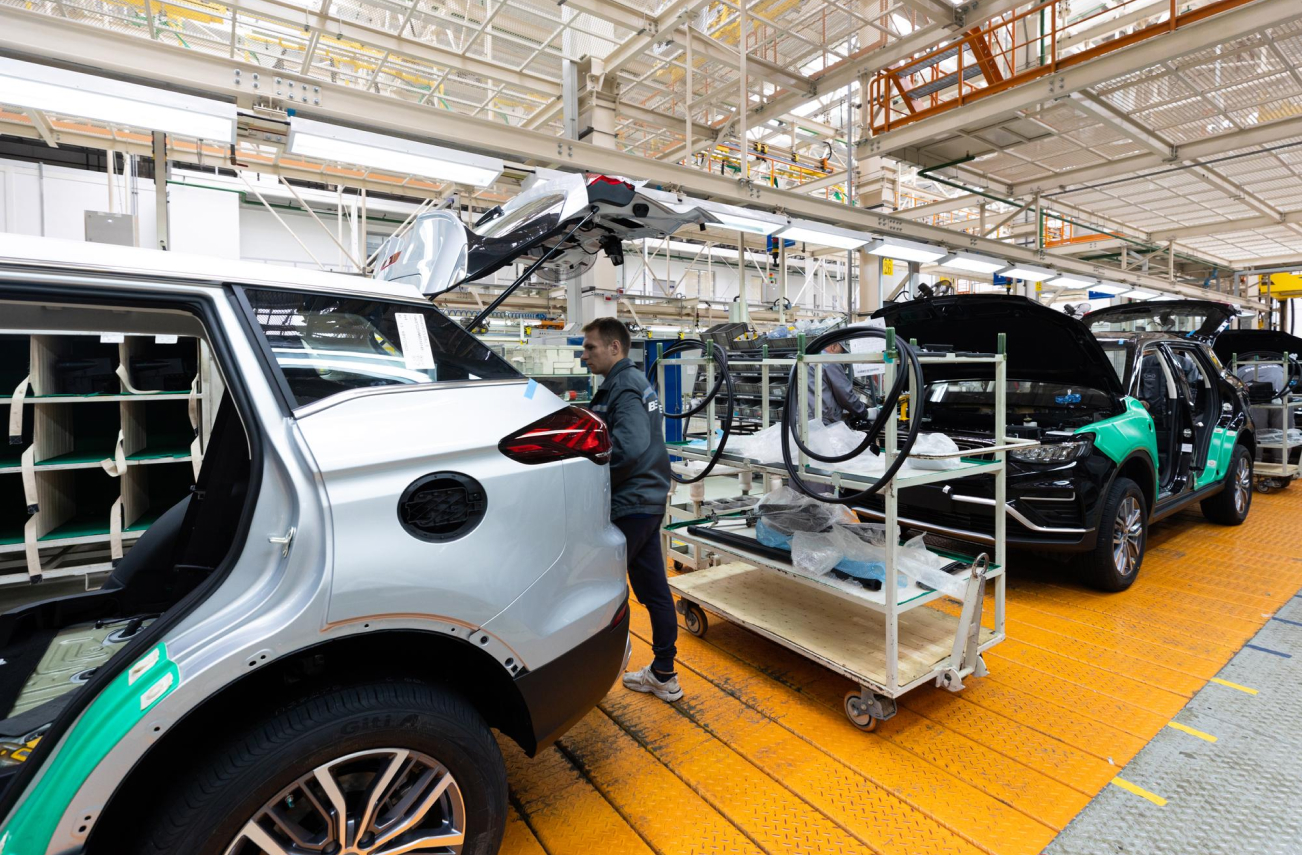
The automotive industry is undergoing a seismic shift towards electric vehicles (EVs). This transition presents both exciting opportunities and significant challenges for manufacturers. Electrify, a fictional car manufacturer, faced the daunting task of scaling EV production while maintaining quality and navigating a complex supply chain. To overcome these hurdles, Electrify embraced digital twin technology, transforming its operations and achieving remarkable results.
The Challenge
Electrify, like many automakers, faced a multi-pronged challenge in its EV transition:
Meeting Production Demands: The surging demand for EVs necessitated a significant increase in production capacity, pushing the limits of existing manufacturing processes.
Maintaining Quality: Scaling up production while ensuring consistent quality across all vehicles was a critical concern, directly impacting customer satisfaction and brand reputation.
Supply Chain Disruptions: Global supply chain issues, particularly impacting the availability of critical EV components, threatened to derail production schedules and jeopardize the company’s ambitious EV roadmap
Design and Engineering
Digital twins played a crucial role in the design and engineering phase. By simulating various EV designs virtually, engineers could thoroughly test aerodynamics, battery performance, and structural integrity. This enabled them to identify optimal design choices early in the development process, reducing the need for costly physical prototypes and accelerating the time-to-market for new electric vehicles.
Production Optimization
Electrify created a digital twin of its assembly line, integrating real-time data from sensors and machines. This virtual representation provided valuable insights. It allowed for the identification of bottlenecks and inefficiencies in the production flow, enabling the optimization of workflows and maximizing throughput. Furthermore, the digital twin facilitated the virtual experimentation of various production scenarios and modifications before implementing them on the physical line, minimizing disruption and risk. Additionally, the digital twin served as a valuable training tool, providing employees with a safe and controlled environment to learn and practice new assembly procedures.
Predictive Maintenance
Digital twins were instrumental in implementing a predictive maintenance strategy. By monitoring the health of manufacturing equipment, the system could predict potential failures before they occurred. This enabled proactive maintenance scheduling, minimizing costly downtime and ensuring uninterrupted production. Moreover, it reduced maintenance costs by servicing equipment only when necessary, optimizing resource allocation. Ultimately, this approach extended the lifespan of manufacturing machinery, maximizing the return on investment.
Supply Chain Management
The digital twin was integrated with supplier data to gain real-time visibility into the status of incoming components. This enhanced supply chain management by enabling the identification of potential delays or disruptions, allowing for proactive risk mitigation and minimizing their impact on production. Furthermore, the digital twin facilitated the dynamic adjustment of production plans, enabling the company to adapt to changing supply chain conditions and ensure uninterrupted operations.
The Results
By leveraging the power of digital twins, Electrify achieved impressive results. Production output increased by 15% within the first year of implementation, while defect rates decreased by 10%. Predictive maintenance reduced unplanned downtime by 20%, leading to a 12% reduction in overall maintenance costs. Furthermore, improved supply chain visibility minimized disruptions, resulting in a 5% increase in on-time deliveries. These quantifiable achievements demonstrate the significant impact of digital twins on Electrify’s operational efficiency and overall success.