Enhancing Productivity and Cutting Costs for an industry leader in electric mobility.
To tackle rising costs and inefficiencies, a major automotive manufacturer upgraded their production with automation and 3D printing.
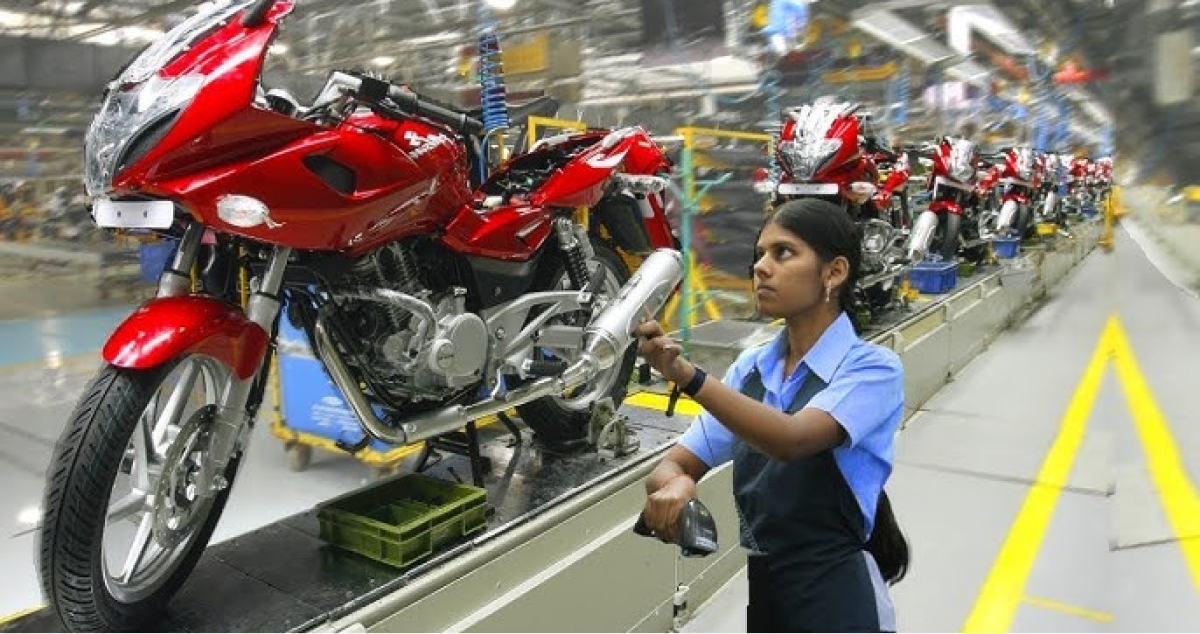
Challenge:
The client struggled with high production costs and inefficiencies caused by outdated machinery and processes. Frequent downtime and material waste were driving up costs and affecting delivery schedules.
Solution:
We implemented a state-of-the-art automation system combined with advanced Additive Manufacturing (3D printing) for rapid prototyping and custom tooling. The project included upgrading machinery and introducing real-time process monitoring to minimize downtime.
Impact:
The project resulted in a 35% reduction in production costs and a 25% increase in overall productivity. Downtime was cut by 40%, and material waste was reduced significantly. The enhanced efficiency and reliability of the production line strengthened the client’s market position.